Column Sides – Pattern Making and Casting
I have started the Gingery shaper project. I am following the instructions in the The Metal Shaper book; however, I will be adapting it to metric dimensions and with metric hardware–at least for the most part. I also know of at least a couple other departures from the design in the book that I am intending to make. I am really excited to start the project, and I hope you are excited to come on this journey with me.
First, I got a lot of questions during my build of the Gingery lathe about how long it took and how much it cost. I intend to do a better job of tracking both during this shaper build. Cost to date are purely fuel since the aluminum and pattern material was scrap. Time to date is 14 hours minimally and 17 hours with optional items like the hoist and unproductive time re-mulling the sand I didn’t cover. Here are the net items from this step.
Fuel Costs | |||||||
Net (kg) | ($/kg) | Cost | Event | ||||
0.23 | 1.22 | $0.28 | Melt Left Side Column Aluminum | ||||
0.23 | 1.22 | $0.28 | Melt Right Side Column Aluminum |
Timesheet | |||||||
Minimum Total | Optional Total | Pattern | Molding | Casting | Cleanup | Machining | Optional |
14:32:14 | 17:11:57 | 6:47:37 | 5:45:23 | 1:59:14 | 0:00:00 | 0:00:00 | 2:39:43 |
Before I could cast the column sides, I had to first make the pattern. The pattern for the mold is a split pattern, and–spoiler alert–there are a lot of split patterns in the book. It seems David discovered split patterns sometime after he designed the lathe because the lathe project doesn’t include any split patterns, and the shaper is full of them. The pattern that I made worked fine for creating the mold, but I am curious if more complex split patterns will separate when I separate the mold halves. With such a small cope half, it really didn’t matter that it stuck to the drag half.
To assist with molding, as part of this part of the project I setup an overhead lift to help in molding. This manually operated lift should improve my ability to roll and separate large molds such as those required to cast the column sides. The hoist is mounted to some scrap wood I used to frame around the HVAC ducting. The host is a couple small diameter pulleys. I bought them at my local big box store, but they are similar to these pulleys. I used some 5/16″ rope–I think I originally bought it as anchor rope for my canoe–to give me a mechanical advantage of 3x. I rigged up a small spreader beam and four small rope legs to attach to the flasks. I used it for molding the column side.
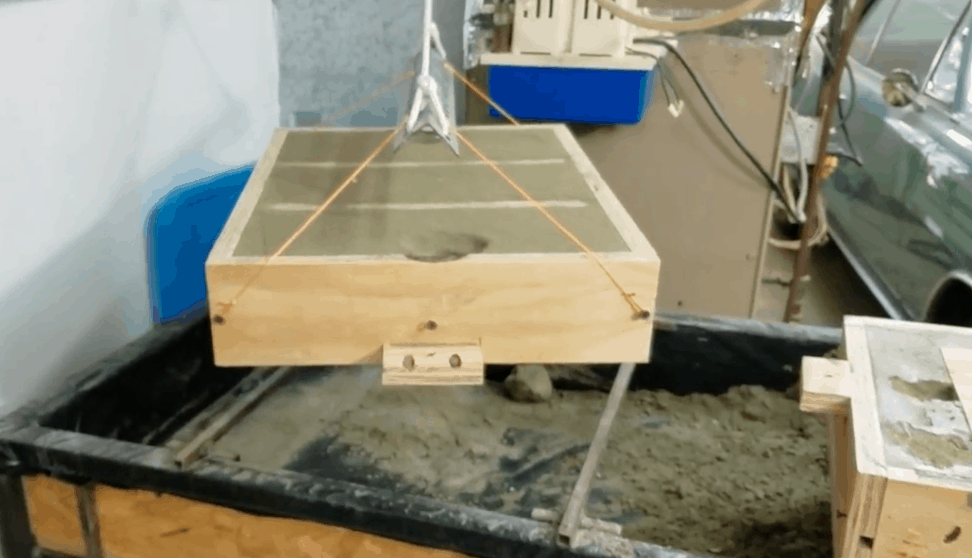
I used my portable propane foundry. Wow! It is so much faster than the kiln. It is not as finely controllable, but 30 minutes from cold to a cast shaper column side is worth the compromise. I used about 0.23kg (0.5lbs)–note I used a scale where this value is the minimum the resolution–of propane to elevate the temperature of 2.25kg of aluminum to about 1400 degrees F from an ambient temperature of 65 degrees F. Because the fuel used was approximately equal to the minimum resolution of my scale, I expect any efficiency calculation would be worthless.
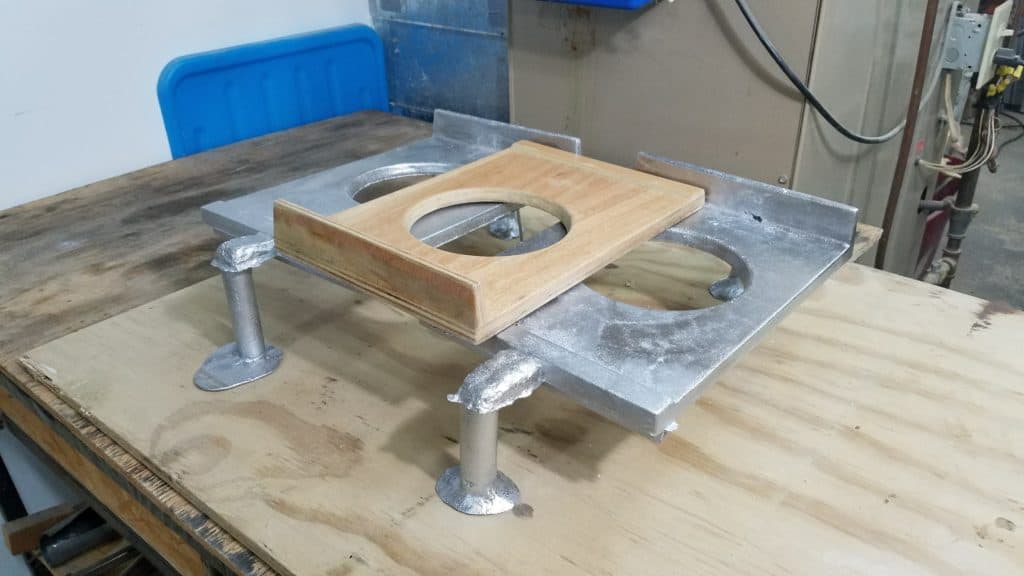
Up next, the column front pattern and casting.
Best video yet! I like the pace of the longer video. Very nice hoist arrangement as well. You mentioned under cost that the aluminum was no-cost scrap; I seem to recall seeing a photo of some old transmission housings. Do you have a “source”, or are those often available at no cost? Junkyard, or auto shop? Thanks for the great videos, looking forward to this series.
I appreciate the kind words. The transmission housings were given to me by a friend. He is moving and decided not to take them with him. You bring up a good point: the material has value even if cash did not leave my hand. I’ll update the post to reflect the scrap value at the time of casting. This will provide a more accurate representation of the relative cost to build. I have purchased metal from scrap yards though I suspect many auto shops would be willing to sell some junk parts for scrap prices too.